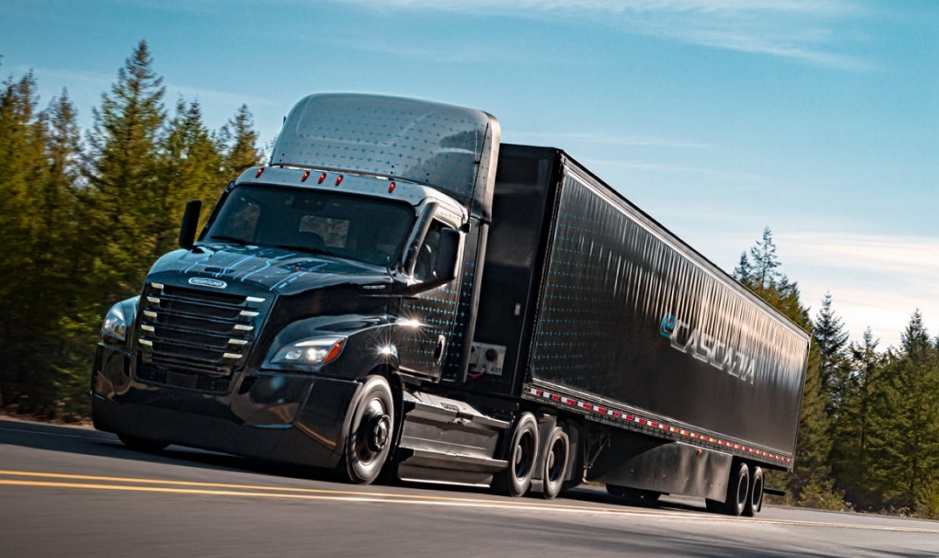
As you arrive at Detroit Diesel Corp. (DDC), now known as “Detroit”, the plant’s website descriptor “It demands to be seen” becomes evident. Located in Redford, Michigan, the iconic Detroit Manufacturing Plant spans over 3 million square feet, which is larger than 52 football fields! This massive facility is responsible for producing an astonishing 500 engines, 250 transmissions, and 1,100 axles every day.
With a rich history dating back to 1938 when it was established as the Detroit Diesel Engine Division, General Motors Co. has a long-standing legacy of producing diesel engines. During World War II, the plant played a crucial role as part of the “Arsenal of Democracy”, supplying compact, two-cycle engines for tanks, landing craft, road-building equipment, and standby generators. By 1943, Detroit Diesel employed over 4,300 people, including over 1,400 women, who worked together to build an impressive 57,892 engines in that year alone.
Now a division of Daimler AG, the company has successfully navigated through significant changes in recent years. Recently, Freightliner, also under the Daimler umbrella, unveiled the production version of their all-electric eCascadia Class 8 truck, following extensive testing of pre-production models with fleet customers. The eCascadia made its debut at the Advanced Clean Transportation Expo in Long Beach, Calif. Designed for short-haul routes with depot-based charging, it is well-suited for last-mile logistics, local and regional distribution, drayage, and warehouse-to-warehouse applications. Powered by the Detroit ePowertrain, it boasts 320 hp in a single eAxle configuration and 470 hp in a tandem design, with three battery options offering a range of up to 230 miles with the largest 440-kWh pack.
The eCascadia features a range of high-voltage (HV) battery options, including a 195-kWh pack with charging times of 1.5 hours to 80 percent capacity and 3 hours to 100 percent capacity, as well as a 291-kWh pack with charging times of 2-4 hours, in addition to the largest 440-kWh pack with charging times of 2-6 hours. These battery packs utilize lithium-ion (Li-Ion) nickel-manganese-cobalt chemistry and are housed in CATL prismatic cells.
However, it’s important to note that the battery assemblies are not small in size. Each eCascadia can have up to 18 modules stacked in three layers of six modules each, with each module containing 18 cells, totaling 108 cells. Despite the size, Detroit’s Li-Ion batteries allow the eCascadia to meet its range targets without compromising payload capacity, which can reach a maximum gross combination weight of 82,000 lbs (37,195 kg), as per the company’s press release.
How to Qualify Battery Assemblers

The demand for the new eCascadia truck has exceeded expectations, with a strong start since the announcement of series production in May. Sysco Corp. wasted no time, signing a letter of intent to purchase 800 eCascadias and integrate them into its fleet by 2026. As Detroit continues to make strides in battery manufacturing, Manufacturing Engineering had the opportunity to visit the pioneering plant and speak with Keith Vaughn, manager of technical services, and Jon Gould, chief electrical specialist and powertrain safety engineer, about their efforts in training and qualifying battery assemblers.
What’s driving the effort to train assemblers?
Keith Vaughn: The effort to train assemblers begins with adhering to safety regulations set by organizations such as OSHA (U.S. Occupational Safety and Health Administration), which requires qualifications for working around live devices. In March 2021, the process of designing benchmark questions and internal assessments was initiated to effectively screen and identify qualified candidates for the battery assembly training program.
Jon Gould: The aim of this effort is to ensure that assemblers are deemed “qualified” to work on batteries, although there is no specific guidance from OSHA or NFPA (National Fire Protection Association) regarding battery assembly requirements. By incorporating best practices and requirements from OSHA and NFPA70E, the goal is to develop a comprehensive training program that defines and attains qualified status for assemblers in the context of battery assembly.
The ultimate objective for our workers is to have a comprehensive understanding of the hazards associated with lithium-ion batteries and the ability to identify and mitigate these hazards, such as through the proper selection and use of personal protective equipment (PPE). Additionally, they need to be knowledgeable about the tools required for safe battery assembly and measurement, including insulated tools and multimeters. It is crucial for team members to demonstrate their proficiency in using these tools to assemble battery modules and determine nominal voltage of both modules and fully assembled batteries. They must also be well-versed in the application of arc flash, limited, and restricted approach boundaries, as well as the identification of exposed energized conductors in specific situations.
Can you describe your program structure and highlights? Is there an ideal candidate profile?
Vaughn: The program starts with an informative session that covers fundamental topics related to the product, process, safety, and operational philosophy. During this session, we provide a comprehensive overview of what DDC will be building and how it will be done. We also explain the training requirements for working in the specific area and outline the expectations for workers in that role. Additionally, we provide detailed information on the next steps for applying and getting into the designated area.
Gould: Following the info session, attendees are sent to our training center to undergo an ePT (electronic pre-employment testing) assessment, which includes basic math and intuition questions. We are looking for candidates who demonstrate an aptitude for learning and a commitment to quality work. Once the assessment is completed, employees are eligible to officially apply for the position. Those who pass the assessment then go through an interview process with the production supervisor, and if successful, they are enrolled in our HV3b course. Passing the exam at the end of this course is a requirement to join the team.
However, at this point, the employee is not yet “qualified” to start assembling batteries. They still need to undergo battery-handling training, followed by “Live Line” training, which focuses on proper selection of PPE and other essential skills. This is the final training required before our workers can be considered fully qualified for battery assembly.
Vaughn: We are seeking employees who take pride in their work and prioritize safety, not just for themselves but also for their colleagues, by consistently following rules and regulations. Teamwork is crucial, and we are looking for candidates who excel in a collaborative environment.
Moreover, we are seeking employees who are enthusiastic about being part of the future of global powertrain. With high expectations, we aim to demonstrate to Daimler and the world that Detroit is ready to meet the challenges ahead and thrive in the evolving automotive industry.
How long is the program, and how is successful completion measured?
Gould: The process of going from the initial info session to becoming a “qualified” battery assembler typically takes about two months, with the training classes spanning approximately one week of that timeline. Through our rigorous selection process, we are able to identify and train enough qualified candidates to meet the demand for battery assembly. We ensure that a suitable percentage of employees successfully complete the selection process and go on to become qualified assemblers in the battery production process.
What did Tooling U-SME contribute? Are there alternative training sources you considered or used?
Vaughn: Tooling U played a crucial role in the development of our HV3b and LLW (Live Line Work) course materials. They expertly tailored the training content to make it accessible and understandable even for individuals without a technical background. Tooling U’s expertise and assistance were invaluable in delivering the initial training classes for both courses, ensuring that our employees received comprehensive and effective training to become proficient in battery assembly and live line work.
Gould: We carefully considered online/computer-based training options, but ultimately concluded that in-person instruction is the best approach for Detroit Diesel. This allows our instructors to connect with our employees in a more effective way, ensuring that the material is well understood. Our instructors are able to gauge the room and provide extra explanations where needed, ensuring that our employees receive the best possible training.
As the demand for our employees to become more technically skilled continues to increase with the addition of alternative powertrain products, we anticipate the need to develop additional courses. We have confidence in our team leaders who are highly skilled and actively engaged in the training process.
Vaughn: Based on the initial test results, we think we hit a home run.