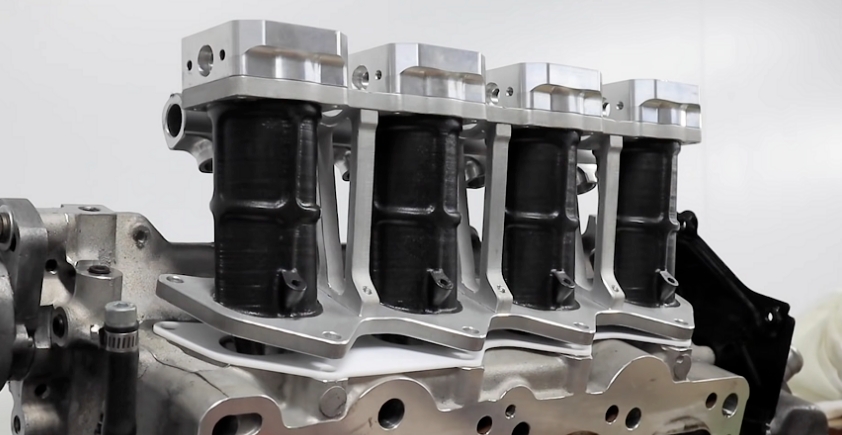
Auto racing is one of the fastest and most technically advanced sports, and the associated manufacturing technologies are at the forefront of innovation. Here’s how Intamsys’ high-temperature 3D printers help create more efficient racing car engine components.
New Zealand-based Hartley Engines and Motorsport designs and manufactures engines and other components for racing teams and small car manufacturers. The company’s customers have won numerous championships in New Zealand and Australia, speed records on the Bonneville salt lake in races with one-liter engines, as well as many awards for innovation in motorsport. Flagship powerplants include Formula One-inspired eight- and twelve-cylinder engines with over a thousand horsepower.
Previously, the company was mainly engaged in the production of engines for the leading racing teams, while the bulk of the work was carried out in strict confidence and only for selected customers. Recently, the company has expanded its scope of activities by supplying engine kits and transferring competencies to other developers, as well as selling components on the open market.
“We realized that we cannot and do not want to create engines for every competitor – we simply do not have enough time. It will be more beneficial for everyone if we open access to our components and developments, ”explains owner Nelson Hartley.

One of the strengths of the company is that it is able to develop products and expand production very quickly. The company’s fleet includes turning and five-axis CNC milling machines, motor dynamometers and even equipment for aerodynamic scavenging. For several years now, Nelson and his team have been honing a hybrid engine manufacturing technique using a combination of milled, carbon fiber and 3D printed parts. One example is reworking throttle bodies using 3D printed air intakes and manifolds.
“From the very beginning, a number of significant advantages of 3D printing were obvious to me. The properties of some of the advanced polymers are very impressive and ideal for things like intake manifolds and other components. When 3D printing the intake manifolds, we use high temperature nylon with 25% carbon fiber (PA-CF). It handles heat better than aluminum, as it conducts heat very slowly, keeping the intake air cold and thus increasing combustion efficiency. An additional plus of 3D printing of manifolds and air intakes is design flexibility. We take the shape of the intake tract very seriously. It’s not just a hole in a plate: thanks to 3D printing, we can reproduce complex curves and shapes from CAD models of cylinder heads.”

In addition to 3D printing finished products, the company also relies on the additive manufacturing of mold tooling, as in the case of the carbon fiber injection chamber in the illustration below. It was not immediately possible to set up 3D printing with high-temperature polymers: before the commissioning of the Intamsys Funmat HT 3D printer with a temperature-controlled chamber, the rejection rate reached 80%.
“We were throwing away more printouts than we could afford: with the cost of consumables up to five hundred dollars per kilogram, plus shipping to New Zealand, there was a question of profitability of 3D printing. After we received our first Intamsys Funmat HT, the defect rate was reduced to five percent! A lot of people in the industry said we couldn’t make mass-produced parts on a 3D printer, but Intamsys equipment proved that wasn’t the case,” says Nelson.
After running the first Intamsys Funmat HT, the company bought a second 3D printer of the same type, and now plans to purchase four more for a new, dedicated additive manufacturing department.

“Our Intamsys Funmat HT cost only one-thirtieth the cost of a five-axis machining center, but the parts we print on it have the same value for customers. So even if 3D printing per part takes longer, I can afford to mass-produce on multiple 3D printers at the same time. In some cases, this is more efficient than installing additional CNC machines. The return on investment in additive technologies has been extremely high. We used to spend hours setting up machines and making tooling just to machine or manufacture one part. Now all I have to do is heat up the Intamsys Funmat HT and hit the start button. No rig is required. Anyone who says that 3D printers will replace all CNC machines is lying, but just as short-sighted is anyone who says that you can’t do production work on an economical 3D printer,” concludes Nelson.