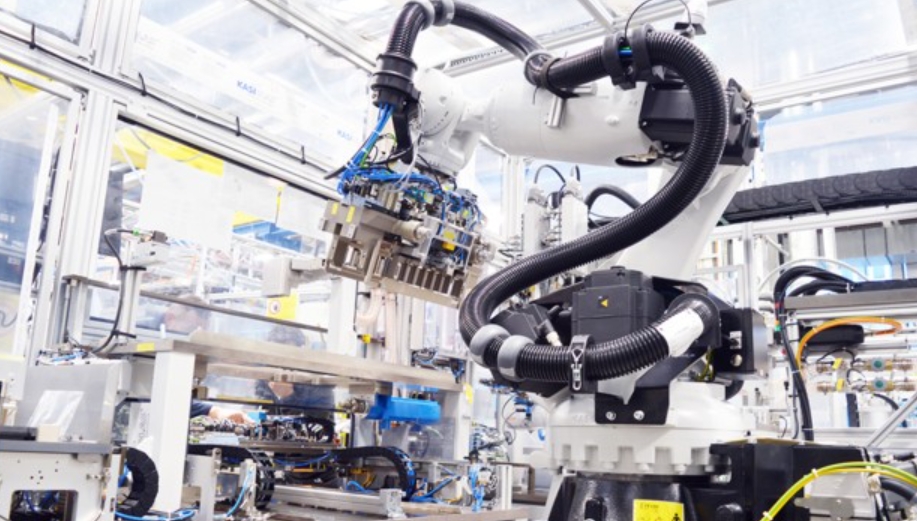
The vast majority of batteries for Europe’s e-cars have so far come from Asia. That is now changing. Not least in Germany, numerous new battery plants are to be built in the coming months, partly by car manufacturers, partly by technology groups. The factories could solve a whole range of geostrategic and practical production problems.
Almost every third e-car worldwide comes from a plant in Europe. But only every tenth battery cell is manufactured here. In the case of the so-called active materials – the basic components of the electrodes – Europe’s market share is only one percent, as a study by the management consultancy PwC recently warned. And the e-car is just about to emerge from its niche. According to the management consultants, the demand for batteries will increase by 35 percent every year until 2030 due to the ramp-up of e-mobility in Europe.
Batteries are a (too) scarce commodity
The European and German manufacturers hesitated for a long time before setting up their own battery or cell production. Instead of investing a lot of money in their own plants, they wanted to buy the electricity storage flexibly. A strategy that obviously reached its limits at the latest with the slow but foreseeable ramp-up of e-mobility towards the end of the last decade. Batteries became a scarce commodity, competition among car manufacturers for the available quantities grew and security of supply became an issue in view of ambitious e-car production plans. The supply chain problems in the course of Corona and the Ukraine war have also made it clear how vulnerable the supply of parts is.
By 2021, almost every battery in a European e-car will come from other Asian countries. This is now slowly changing, but should soon pick up speed. Numerous companies have already announced large battery plants on the continent: If the plans are implemented, the annual production in 2030 will be 1309 gigawatt hours, as scientists from the “Production Engineering of e-Mobility components” chair at the RWTH Aachen University have calculated.
VW wants to build “unit cell” on a large scale
Volkswagen in particular wants to set up battery and cell production on a large scale in Europe. By 2030, six production plants with an annual capacity of 240 gigawatt hours are to be put into operation together with partners. The car manufacturer wants to build the first new plant together with Northvolt in Sweden by 2023 and build cells for premium models there. The gigafactory in Salzgitter, operated by Volkswagen itself, is to produce the unit cell for the volume segment from 2025. Other factories follow.
Germany will be the largest battery manufacturer in Europe, where, in addition to VW and Tesla, companies such as CATL, Varta, Svolt, CALB, ACC, Blackstone Resources and Northvolt are also planning plants. If all the announcements are implemented, plants with a capacity of 478 gigawatt hours (GWh) will be built here in the coming years. For comparison: Global battery production for electric cars was an estimated 286 GWh in 2021. The largest single manufacturer was the Chinese group CATL with 87.8 GWh ahead of LG and Panasonic.
Close production brings advantages
Not only logistics and geostrategy speak for the battery and cell production on site. Also much more concrete and practical considerations. Car manufacturers are currently suffering from not having their battery suppliers in the local area like almost all other suppliers. Joint developments or short-term adjustments are difficult to implement in this way. For a long time, car manufacturers therefore had to buy off the peg from the Asians what they had in their wide range, which was also characterized by entertainment electronics. “One cell for all” was the motto of the battery manufacturers. In the future, however, car manufacturers would prefer to have custom-made products. The German premium manufacturers in particular could set themselves apart from the volume competition with special formats, for example. Luxury cars like the Porsche Taycan already use specially tailored battery packs that are less bulky than the standard modules and thus allow a particularly flat body.
Recycling lags behind
The recyclability in Europe would probably also benefit. So far, the Asians have also been leaders in this respect, since they have sufficient practice material with the waste from their cell plants to work on recycling. We largely lack this know-how, at least on an industrial scale. In general, basic research and development are strong in this country, but transferring them to a large scale is considered to be very difficult, especially in cell production.
Car manufacturers need not be afraid of excessively high production costs outside of Asian low-wage countries. Around 70 percent of the battery costs are attributable to the material, personnel essentially only required for monitoring production, so wages only play a secondary role in the balance sheet. It is likely to become more difficult to refine the manufacturing process in such a way that the cost-intensive material waste is kept to a minimum.